蜂巢能源董事長兼CEO楊紅新表示:市場并不缺動力電池產能,但缺的是車規(guī)級高品質動力電池產能。蜂巢能源將推行電動全域短刀化。
車規(guī)級的高品質短刀電池究竟是如何生產出來的?
2月25日,部分媒體代表應邀參觀蜂巢能源金壇工廠,零距離探訪蜂巢能源“短刀”電池的智能制造過程。
蜂巢能源在全球規(guī)劃了11個生產基地,金壇園區(qū)為蜂巢能源建設的首個車規(guī)級動力電池AI超級工廠,共分四期建設,總產能規(guī)劃為68GWh。目前,一期、二期工廠已經正式投產,在二期工廠中建設了首條“短刀”電池量產線,滿產產能將達到2.5GWh。
蜂巢能源董事、工藝資深總監(jiān)劉小安向來訪媒體介紹,脫胎于整車企業(yè)的蜂巢能源,從成立一開始就對于整車的應用場景和標準有更深入的理解,因此在建立金壇工廠時就充分考慮了車規(guī)級應用標準,率先建成行業(yè)領先的車規(guī)級AI智能工廠。
劉小安表示:汽車上使用的零部件都要伴隨整車應對各種各樣的路況、環(huán)境、溫度、濕度等等,使用期限在8-10年以上,所以對產品的可靠性都有超高的要求,因此,車規(guī)級也就代表著產品的可靠性。
他進一步解釋,車規(guī)級主要是體現在工廠的管控嚴苛程度,蜂巢能源車規(guī)級電池工廠從電池產品生產過程中的異物管控,到毛刺控制,從AI智能技術的應用,到先進裝配技術的應用和集成化工藝的應用,最終目的就是為了保證生產出符合汽車使用的高品質電池產品。比如蜂巢能源廠房潔凈度采用萬級潔凈度控制標準,局部實現千級控制,達到芯片級生產的潔凈度標準。濕度控制上,從投料-電芯封口全制程1%濕度管控。
動力電池走向大規(guī)模制造過程中,如何在保證產品品質的同時提升核心生產工序的效率是行業(yè)面臨的共同挑戰(zhàn)。圍繞于此,蜂巢能源短刀電池工廠通過工序優(yōu)化和工藝創(chuàng)新,不僅實現了電池更為嚴苛的品質管控,也大幅提升了生產制造效率。
勻漿、涂布、輥壓、模切、疊片、裝配六大工序是短刀電池的生產過程中的主要環(huán)節(jié),每一個環(huán)節(jié)的表現都直接決定最終產品的安全和性能發(fā)揮。記者在工廠實地探訪過程中發(fā)現,蜂巢能源圍繞這六大工序做了一系列的獨家創(chuàng)新。
勻漿
要實現短刀電池的大規(guī)模量產,首先要確保漿料的大規(guī)模生產。劉小安提到,蜂巢能源在勻漿環(huán)節(jié)采用2300L大容量雙行星攪拌設備,目前該設備單體容量行業(yè)領先,適合車用動力電池大規(guī)模生產,每罐漿料生產的電池可配套純電動車約10輛左右,更大的勻漿設備確保了產品品質和大規(guī)模工業(yè)化量產的一致性。
為了提升品質管控,蜂巢能源在漿料輸送環(huán)節(jié)比行業(yè)通行標準多加了一道除磁工序,從而使得漿料級磁性異物含量可以做到50ppb以下(磁性異物重量占比十億分之五十),高出行業(yè)水平50%。
涂布
短刀電池的長度比普通電芯更長,涂布的寬幅、速度、精度決定了短刀電池極片生產的效率和品質,蜂巢能源采用1400mm超寬幅涂布機,一次出兩列,涂布速度高達80m/min,處于行業(yè)領先水平。而且為了保證涂布精度,蜂巢能源在涂布設備上設置三套β射線在線面密度檢測系統(tǒng)和2套CCD實時涂寬檢測系統(tǒng),實現數據實時檢測和控制,并達到自動閉環(huán)管控,涂布面密度可控制在±1.5%以內,涂布正反面錯位≤0.5mm。
輥壓
在輥壓工序,蜂巢能源通過正極熱輥壓,負極雙輥連續(xù)滾軋,正極輥壓速度80m/min,在輥壓機上進行電磁加熱、紅外線在線烘烤、在線激光測厚、廢料邊去除等技術集成,通過簡化工藝實現更高效率。
模切
在模切工序,最大的挑戰(zhàn)來自于效率和成本,與行業(yè)主流的五金模切不同,蜂巢能源在該環(huán)節(jié)全部應用了激光模切,不僅節(jié)省了模具投入和設備維護的費用,模切效率也得到大幅提升,由原來的30m/min,提升至40-50m/min,效率提升40%。劉小安還透露,下一個短刀產線會采用更加先進的設備,工藝進一步集成,效率也將大幅提升。
疊片
對于采用疊片工藝的電池生產,疊片速度一直是行業(yè)痛點,而蜂巢能源一直引領高速疊片工藝,目前采用的采用雙工位疊片效率高達0.4s/片,已經達到業(yè)內領先水平。同時,已研發(fā)完成的下一代超高速刀片式電芯極組成型設備,疊片效率可以做到0.125s/片,一舉超越卷繞極組成形效率,引領全球短刀片電芯的生產效率。
在極組物流運輸環(huán)節(jié),短刀電芯單極組的重量、長度尺寸是其它極組的1至2倍,因此對疊片至熱壓轉運過程中極組對齊度的保證要求更高,傳統(tǒng)的皮帶物流線很難勝任要求,針對此,蜂巢能源在行業(yè)內率先導入使用了磁懸浮物流線。相比于傳統(tǒng)皮帶物流線,磁懸浮物流線傳輸效率更高,可以達到皮帶物流線的10倍,同時,磁懸浮運輸車的加減速更加均勻,極組對齊度更易保證。此外,磁懸浮采用潤滑滾動,相比于皮帶線的滑動干摩擦,可以減少異物,且一致性更高,無碰撞問題,異物抑制率提升80%。
異物管控和焊接是裝配環(huán)節(jié)的兩大核心。為了保證裝配過程的品質,蜂巢能源在電芯整個裝配過程設置了4次hipot測試,產品異物的檢出能力遠高于行業(yè)2-3次的水平。顆粒物檢測級別由業(yè)內200微米提升至50微米水平。而為了解決刀片電芯最難的周邊焊接問題,蜂巢能源采用對縫焊接,正負極同時周邊焊接,提升焊接效率50%以上,同時,采用超高速焊縫自動追蹤焊接工藝,提升焊接良品率10%以上,焊接速度可以達到200mm/s。
為了保證高質量高效率的生產,蜂巢能源在現場管控還做了很多的措施,這包括導入極組入殼前少抓取設計、防止劃傷和過程變形的設計等,在基于蜂巢能源車規(guī)級AI智能動力電池工廠的各項標準,最終保證了短刀電池的規(guī)?;慨a。
參觀過程中,蜂巢能源的各種創(chuàng)新科技引用令人大呼“太牛了!”
以數字化、網絡化和智能化為核心特征的新一代信息技術正在與動力電池制造深度融合,在蜂巢能源短刀電池工廠里, AI技術的應用隨處可見。
參觀隨行的AI技術相關負責人介紹,蜂巢能源已經通過AI大數據分析進行質量智能檢測,實現質量檢測的智能化及無人化,利用人工智能將不良品的分類與工藝參數結合,自動尋找最佳參數,節(jié)約開發(fā)時間30%,智能化的設備健康管理,維護先期預警可以降低故障率提高設備稼動率。
蜂巢能源的思路是,通過利用人工智能、先進分析和邊緣/云計算等技術,對于效率提升、品質提升、碳追溯等各個環(huán)節(jié),都將會起到至關重要的作用。
面向TWh時代,對于動力電池企業(yè)而言,要實現車規(guī)級高品質的動力電池產能和高效高質量交付,就需要不斷革新制造工藝、更為嚴苛的把控生產過程,并通過智能化賦能制造。
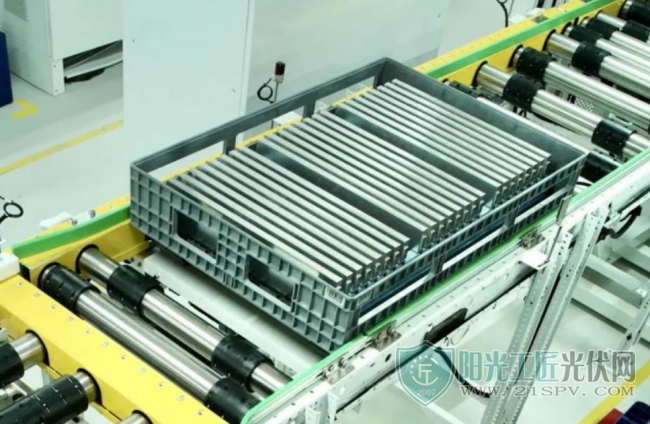
蜂巢能源短刀電池
作為率先在行業(yè)落地建設車規(guī)級AI智能動力電池工廠的企業(yè),蜂巢能源的工廠在設計之初就在上述各項指標上設置了遠超國標的嚴苛標準,其關鍵生產工序進行了一系列工藝技術創(chuàng)新,大量采用AI智能技術應用,確保了產能的優(yōu)質高效和產品的高質量。
原標題: 首次揭秘蜂巢能源短刀電池超級工廠